FUEL & FUEL SYSTEM MICROBIOLOGY PART 6 – HANDLING SAMPLES
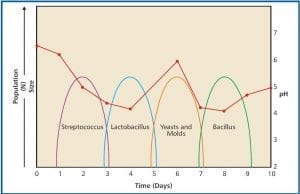
Fig 2. Microbial population succession in Milk. Source: CAERT
Today, I’m returning to the sampling issue that I introduced in Part 2. In particular, I’ll focus on the concept of sample perishability – the tendency for the contents or properties of a sample to change over time.
Microbes are living beings. Like all other living beings, microbes eat, discharge (excrete) wastes, use energy, grow (individual cells get larger), reproduce (proliferate), and respond to their environment. Samples are perishable because microbes collected in the sample, continue their activities after they have been captured. They respond to their environment and change it, by using up nutrients and excreting wastes.
Even before active microbes change them, conditions in a sample container are different from those in the system from which the sample was collected. As a result, microbial populations in sample containers can change in three basic ways: 1) the total number of microbes can change: increasing, decreasing, or remaining approximately the same (in the last case, the number of new cells produces is approximately equal to the number of cells dying); 2) the relative abundance of different types of microbes can change; and 3) the combined (interaction) impacts of these two factors can alter the microbial population in countless ways.
Total bioburden: Figure 1 shows how the total number of cells (bioburden) in a fuel + bottoms-water sample can change as the delay between sampling and testing increases. Because of these changes, ASTM D7464 recommends that samples be tested within 4h after collections and notes that after 24h, even refrigerated samples are unlikely to have microbial populations that closely resemble those present immediately after the sample was collected.
Relative abundance: Types of microbes that were a major part of the total population in the system from which the sample was collected, are sometimes less able to adapt to the conditions in the sample bottle. When this happens, both the diversity (number of different types of microbes) and the relative abundance (percentage of the total population each type of microbe represents) can change. Look at Figure 2. Over the course of the first week or so, after milk is collected, there are typically four major population shifts. For our purposes the population succession details are unimportant. What is important is that milk’s microbial population changes dramatically. The population succession in fuel and fuel-associated water samples has not been well studied, but the evidence that does exist suggests that it does occur.
Bottom line: Fuel system samples are perishable because the population beings to change so quickly after samples are collected. For routine condition monitoring, relative abundance changes aren’t going to affect your action decisions. However, if the population either increases or decreases dramatically between the time the sample was collected and the time it was tested, operators risk either taking action when it is not needed or failing to take action when it is. To learn more about fuel system sampling for microbial contamination control, please contact me at fredp@biodeterioration-control.com.